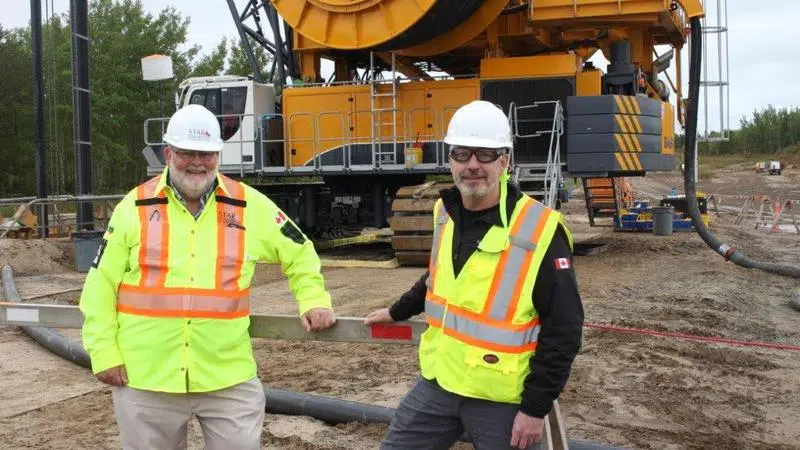
Special Feature: The people behind the quest for Fort à la Corne’s diamonds
The first season of deep trench-cutting by Rio Tinto at Star Diamond Corporation’s Star-Orion South Diamond Project in the Fort à la Corne forest east of Prince Albert is reaching a conclusion. Ahead of the next element of the mining giant’s initial exploration phase, paNOW’s Glenn Hicks and photographer Ian Gustafson visited the site to speak to some of the people doing their part to unlock the treasure.
If you blink heading East where the signpost says Shipman, you’ll miss it. To the left of this intersection in the middle of nowhere are remnants of sad-looking properties. The population is numbered at 10, and that seems generous. This tiny hamlet saw better days when there was a sawmill, and then in the 1930s when there were farming opportunities. It once had three grocery stores, a restaurant, poolroom and community hall according to writer David McLennan.
But it’s the right hand turn on this stretch of Highway 55 that points to a whole different and potentially brighter picture for this region, Prince Albert, and the province. The 45-minute drive South along the dirt road leads to what Rio Tinto refers to as Project Falcon, a possible joint venture between them and Star Diamond that could – and that’s a big multi-faceted ‘could’ – create hundreds of full-time jobs and generate billions of dollars.
The journey through the unique island of green that is the Fort à la Corne forest is punctuated by sightings of chipmunk and deer. Coyotes and wolves are among the other fauna that roam here. However, it’s the final turn in the road that reveals a beast that leaves no doubt about the enormity of the efforts underway to unearth what Star Diamond Corp. figures are 66 million carats of precious stones presently estimated to be buried far below the thick challenging surface here. The towering Trench Cutter Sampling Rig is the first thing you see when you enter the sprawling site.